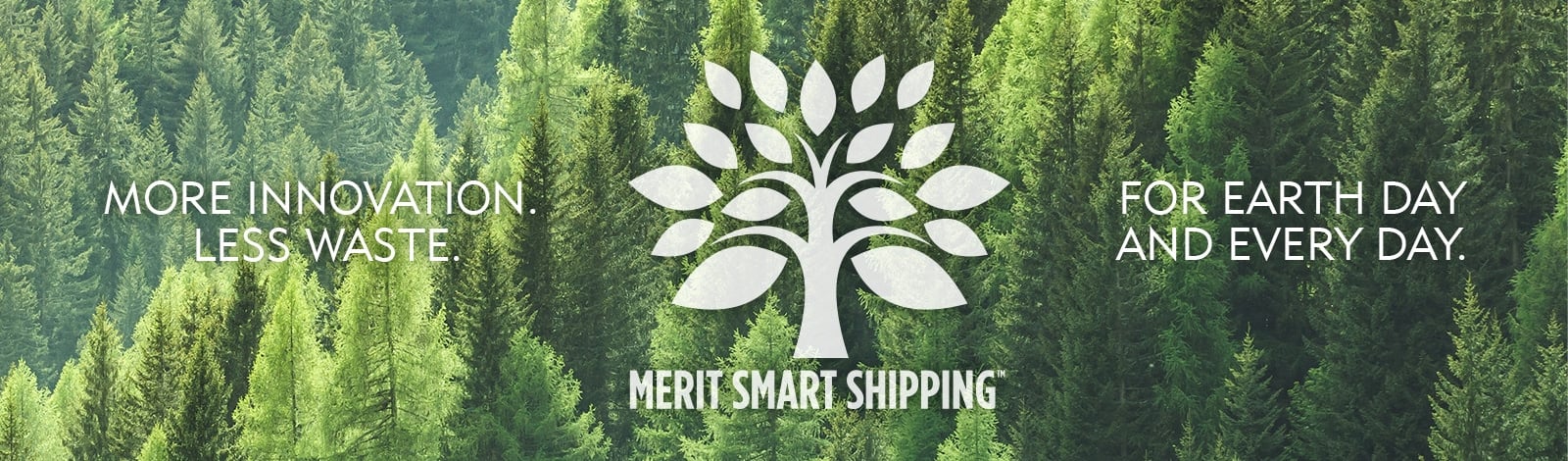
Several Merit products are available to ship through Merit Smart Shipping™, a program designed and tested to ship products in their own packaging, eliminating the need for additional packaging materials. This green initiative has saved 72 tons of corrugated box material per year, a number that continues to grow as more products are added to this program.
“Merit Smart Shipping places products into packaging that does not require any additional handling or over-packaging at the point of shipment,” says Matt Wold, Director of Packaging Engineering at Merit Medical. “Having to use additional boxes, bubble wrap, or paper dunnage to our finished goods before they ship is wasteful, time-consuming, and expensive.
”The U.S. Environmental Protection Agency reports that containers and packaging make up a major portion of municipal solid waste, with corrugated boxes being the largest single product category of waste.1 Even after considering additional statistics, such as amount recycled, 1.9 million tons of corrugated boxes ended up in landfills in 2015.1
To reduce the amount of packaging that products require to ship, our management and packaging engineering teams came together with our shipping department at Merit Medical’s global headquarters in Salt Lake City, Utah, to design something smarter: Merit Smart Shipping.
“We began developing and qualifying the Merit Smart Shipping program in 2015,” Mr. Wold explains. “A packaging engineer first develops a design for the new Merit Smart Shipping box then conducts a formal simulated shipping study to qualify it.
”The first product changed to Merit Smart Shipping was the MAK™ Mini Access Kit. Originally, the product was packaged using an E-Flute carton that required extra over-packaging as well as a larger over-shipper box that involved a significant amount of paper dunnage to keep the carton from moving.
“Merit Smart Shipping boxes take the place of the over-packaging box, and paper dunnage isn’t required,” Mr. Wold says. “The products are placed into these boxes during production and then shipped to customers without having to handle the boxing again.”Since that first MAK product in 2015, many other products and product families (including the entire MAK product family) have been qualified to use Merit Smart Shipping boxes, such as Resolve®, Impress®, Performa®, Merit Maestro®, SwiftNINJA®, and FirstChoice™.
According to Mr. Wold, this shift saves 72 tons of corrugated box material per year, resulting in a win-win for both Merit and its customers.
“Customers have to place fewer boxes and less packaging material into the hospital waste system,” Mr. Wold says. “And Merit uses less corrugated material each year. This not only saves time and money, it also reduces our carbon footprint.
”Merit Smart Shipping™ will continue as part of our global Merit Environmental Sustainability effort.
REFERENCES
- United States Environmental Protection Agency. (2015). Facts and figures about materials, waste and recycling. (Containers and packaging: Product-specific data). Retrieved from https://www.epa.gov/facts-and-figures-about-materials-waste-and-recycling/containers-and-packaging-product-specific-data#PaperandPaperboardC&P